Technical Information
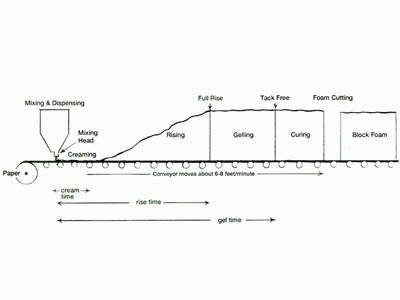
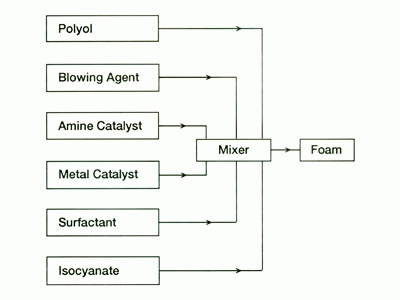
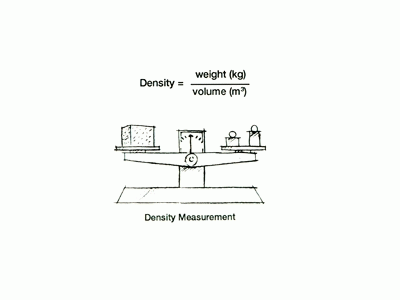
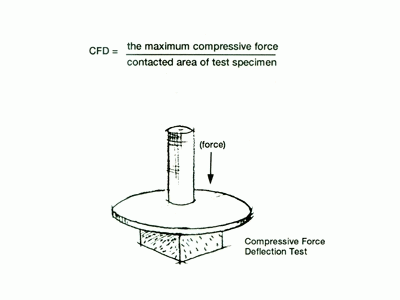
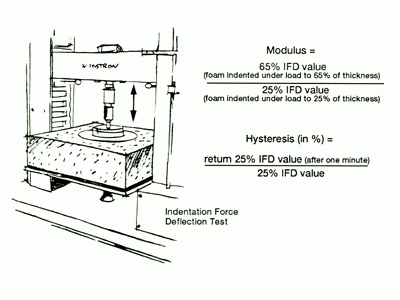
Foaming of Flexible Slabstock Foams
In the first of several distinct, sequential events in polyurethane foaming, the ingredients are dispensed in appropriate proportions, usually through a metering device, and mixed (See diagram 1). Mixing generates tiny gas bubbles in the liquid mixture in a process called nucleation. As the bubbles enlarge, the surface of the liquid becomes lighter in color and has a creamy appearance. The time from mixing to creaming is known as the cream time.
Diagram 1- Typical Reaction Profile for Flexible Slabstock Foam
Figure 21
As more blowing gases are generated, the foaming mixture continues to expand and thicken, but the total number of bubbles remains constant as the foam rises. The evolution of gas ceases as gelling progresses from one to three minutes after mixing. As the cells gradually strengthen, internal pressure forces the gases out of the foam, which is now strong enough to remain standing. The time required for this to occur is called the blow-off time. The time from the start of the reactions to full foam rise is called the rise time.
The exothermic reactions of isocyanates with water and polyols, which are accelerated by the presence of catalysts, account for most if not all, of the heat generated during and after foaming. Scorching (a brown discoloration of the foam, particularly in the center area) can occur whenever excessive heat is generated by the reaction.
The gelling reaction, or polymerization, continues and the foaming mixture progresses from a liquid to a dry solid. The time required for this to occur is known as the gel time. To test whether a foam bun has gelled, the operator repeatedly inserts a wooden spatula into the gelling mass. When the outer skin of the foam no longer adheres to the spatula on gentle touching, the tack free time has been reached.
Once formed, foam blocks are cut and transferred to a curing area, where they are allowed to stand separately for at least 24 hours. If the cut surface of a foam feels velvety, the foam is said to have a good "hand". If it is harsh or rough to the touch, the foam is said to have a poor hand. Shrinkage can occur as the foam cools down. During cooling, catalyst and isocyanate vapors are liberated, so, for worker safety, the storage area must have good ventilation, a water sprinkler system, reasonable separation from other buildings, and easily accessible exits. A well-cured foam block will burn if exposed to an external ignition source, such as a cigarette, electrical spark, motor vehicle exhaust, or an open flame. As a result, foam blocks should always be stored away from possible external ignition sources.
Foaming Processes
Diagram 2- Foam Production - One-Step Process
figure 22A
Several techniques are used to control the polyurethane reaction. More specifically, polyurethane foams can be prepared by means of a one-step, a two-component, or a prepolymer process.
Most foams are produced by the one-step process (See diagram 2). Here, all the reactants are simultaneously metered, mixed, and dispensed onto a conveyor or into a mold. Nearly all modern flexible slabstock (continuous foam) machines are designed on this basis.
Foam Density
An important physical property of foam is its density. Density is controlled by the amount of blowing agent, water, or chorofluorocarbon used in the formulation. The density of a foam block is not uniform, especially in larger blocks; it is greatest at the bottom and generally lowest near the surface. Density is calculated by using the volume of the material after foaming. A foam sample of regular shape and reasonable size is weighed and measured. Its density may then be calculated using the following equation:
Density Measurement
CFD and IFD Rating Systems
A common method for varying slabstock foam's hardness or load-bearing characteristics (its resistance to compression and indentation) is to adjust the isocyanate index. This changes the number of isocyanate groups available for cross-linking. MDI-based foams can be made stiffer at the edges than at the center by changing the foam reaction mixture as it is dispensed into the mold.
Certain tests help measure a foam's hardness. In compression force deflection (CFD) tests, a standard-size foam specimen with parallel flat faces is held between two larger parallel plates. The force required to compress the foam at a constant rate to a specific percentage of thickness is measured. The compressive strength of a material is the value of the maximum compressive force divided by the contacted surface area of a defined test specimen.
CFD test IFD test
An indention force deflection (IFD) test classifies many flexible, cellular polyurethane materials. IFD is a measure of the load-bearing properties of foam intended for seating, bedding, and other cushioning applications. In the standard test, a 50-square-inch indentor foot is depressed into the foam and the number of pounds required to achieve a desired deflection is measured.
From the initial data, two additional factors may be calculated: the modulus (also known as the sag factor), which measures comfort, and the hysteresis, which measures foam recovery after deflection.
Glossary of Terms
Density: The density of a piece of foam is basically the weight of the foam. It is determined by weighing one cubic foot of the foam (a piece that is 12"x12"x12"). Generally, the higher the density, the longer the foam will last and the more it will cost.
I.F.D. (Indent Force Deflection): This is a measurement of firmness. The standard test is to depress a 50-square inch indenter foot into a foam sample that measures 4"x15"x15". The amount of force that is required to compress the sample from 4" to 3" is known as the I.F.D. or 'compression'. A foam that requires 40# of pressure is commonly known as a 40# foam.
H.R. (High Resilient) Foam: A premium cushioning foam that is produced by blending certain 'polyol' chemicals. H.R. foams generally have a different (more open) cell structure than do conventional foams. This unique cell structure adds to the longevity and durability of the foam.
High Density Foam: 'High Density' is a term usually reserved for a conventional foam product that has a density of 1.8# or more.
Board Foot: The most common unit of measurement used when calculating the size and/or pricing of urethane foam. The board feet involved in any piece of foam is determined by multiplying the length X width X thickness and then dividing that result by 144. When you multiply that result by the board foot price it will result in the per piece price of the cushion.
Fire Retardancy Codes (As it related to Foam)
MVSS 302: Motor Vehicle Safety Standard #302...This regulation is an automotive fire specification covering materials being installed into the interior of cars, trucks, buses, and recreational vehicles.
Technical Information
Foaming of Flexible Slabstock Foams
In the first of several distinct, sequential events in polyurethane foaming, the ingredients are dispensed in appropriate proportions, usually through a metering device, and mixed (See diagram 1). Mixing generates tiny gas bubbles in the liquid mixture in a process called nucleation. As the bubbles enlarge, the surface of the liquid becomes lighter in color and has a creamy appearance. The time from mixing to creaming is known as the cream time.
Diagram 1- Typical Reaction Profile for Flexible Slabstock Foam
Figure 21
As more blowing gases are generated, the foaming mixture continues to expand and thicken, but the total number of bubbles remains constant as the foam rises. The evolution of gas ceases as gelling progresses from one to three minutes after mixing. As the cells gradually strengthen, internal pressure forces the gases out of the foam, which is now strong enough to remain standing. The time required for this to occur is called the blow-off time. The time from the start of the reactions to full foam rise is called the rise time.
The exothermic reactions of isocyanates with water and polyols, which are accelerated by the presence of catalysts, account for most if not all, of the heat generated during and after foaming. Scorching (a brown discoloration of the foam, particularly in the center area) can occur whenever excessive heat is generated by the reaction.
The gelling reaction, or polymerization, continues and the foaming mixture progresses from a liquid to a dry solid. The time required for this to occur is known as the gel time. To test whether a foam bun has gelled, the operator repeatedly inserts a wooden spatula into the gelling mass. When the outer skin of the foam no longer adheres to the spatula on gentle touching, the tack free time has been reached.
Once formed, foam blocks are cut and transferred to a curing area, where they are allowed to stand separately for at least 24 hours. If the cut surface of a foam feels velvety, the foam is said to have a good "hand". If it is harsh or rough to the touch, the foam is said to have a poor hand. Shrinkage can occur as the foam cools down. During cooling, catalyst and isocyanate vapors are liberated, so, for worker safety, the storage area must have good ventilation, a water sprinkler system, reasonable separation from other buildings, and easily accessible exits. A well-cured foam block will burn if exposed to an external ignition source, such as a cigarette, electrical spark, motor vehicle exhaust, or an open flame. As a result, foam blocks should always be stored away from possible external ignition sources.
Foaming Processes
Diagram 2- Foam Production - One-Step Process
figure 22A
Several techniques are used to control the polyurethane reaction. More specifically, polyurethane foams can be prepared by means of a one-step, a two-component, or a prepolymer process.
Most foams are produced by the one-step process (See diagram 2). Here, all the reactants are simultaneously metered, mixed, and dispensed onto a conveyor or into a mold. Nearly all modern flexible slabstock (continuous foam) machines are designed on this basis.
Foam Density
An important physical property of foam is its density. Density is controlled by the amount of blowing agent, water, or chorofluorocarbon used in the formulation. The density of a foam block is not uniform, especially in larger blocks; it is greatest at the bottom and generally lowest near the surface. Density is calculated by using the volume of the material after foaming. A foam sample of regular shape and reasonable size is weighed and measured. Its density may then be calculated using the following equation:
Density Measurement
CFD and IFD Rating Systems
A common method for varying slabstock foam's hardness or load-bearing characteristics (its resistance to compression and indentation) is to adjust the isocyanate index. This changes the number of isocyanate groups available for cross-linking. MDI-based foams can be made stiffer at the edges than at the center by changing the foam reaction mixture as it is dispensed into the mold.
Certain tests help measure a foam's hardness. In compression force deflection (CFD) tests, a standard-size foam specimen with parallel flat faces is held between two larger parallel plates. The force required to compress the foam at a constant rate to a specific percentage of thickness is measured. The compressive strength of a material is the value of the maximum compressive force divided by the contacted surface area of a defined test specimen.
CFD test IFD test
An indention force deflection (IFD) test classifies many flexible, cellular polyurethane materials. IFD is a measure of the load-bearing properties of foam intended for seating, bedding, and other cushioning applications. In the standard test, a 50-square-inch indentor foot is depressed into the foam and the number of pounds required to achieve a desired deflection is measured.
From the initial data, two additional factors may be calculated: the modulus (also known as the sag factor), which measures comfort, and the hysteresis, which measures foam recovery after deflection.
Glossary of Terms
Density: The density of a piece of foam is basically the weight of the foam. It is determined by weighing one cubic foot of the foam (a piece that is 12"x12"x12"). Generally, the higher the density, the longer the foam will last and the more it will cost.
I.F.D. (Indent Force Deflection): This is a measurement of firmness. The standard test is to depress a 50-square inch indenter foot into a foam sample that measures 4"x15"x15". The amount of force that is required to compress the sample from 4" to 3" is known as the I.F.D. or 'compression'. A foam that requires 40# of pressure is commonly known as a 40# foam.
H.R. (High Resilient) Foam: A premium cushioning foam that is produced by blending certain 'polyol' chemicals. H.R. foams generally have a different (more open) cell structure than do conventional foams. This unique cell structure adds to the longevity and durability of the foam.
High Density Foam: 'High Density' is a term usually reserved for a conventional foam product that has a density of 1.8# or more.
Board Foot: The most common unit of measurement used when calculating the size and/or pricing of urethane foam. The board feet involved in any piece of foam is determined by multiplying the length X width X thickness and then dividing that result by 144. When you multiply that result by the board foot price it will result in the per piece price of the cushion.
Fire Retardancy Codes (As it related to Foam)
MVSS 302: Motor Vehicle Safety Standard #302...This regulation is an automotive fire specification covering materials being installed into the interior of cars, trucks, buses, and recreational vehicles.
Cal Tech 117: California Technical Bulletin #117... This regulation is a furniture fire specification established by the California State Fire Marshall covering the materials that are being used in the production of furniture that will be sold in the state of California. Many other states require compliance to the regulation in the production of, and the upholstery of furniture.
Cal Tech 117: California Technical Bulletin #117... This regulation is a furniture fire specification established by the California State Fire Marshall covering the materials that are being used in the production of furniture that will be sold in the state of California. Many other states require compliance to the regulation in the production of, and the upholstery of furniture.